Experiences Gained
Time Management
Time management was a key factor in the manufacture process of making the speaker. Having six weeks to complete the project was going to be tough especially as there was problems and errors that occured. I planned out in my head what i would do and when so i would always have something to do. I found this was helpful as i was able to use all the lesson time to its full potential. Looking back it would have been more productive for me if i had printed off my plan of manufacture and used that instaed of thining on the spot. It was clear to me that i was never going to finish the speaker in the lesson time that was given so i had to use my free periods to make my speaker by the deadline.
Tools, Processes & Machinery
In the whole process of manufacture I used a wide range of tools to make my speaker. The band saw was one of the main tools that I used as it was big enough to cut the shape that I needed unlike the Hegnar saw which was to small to cut the curves. in the front and back shape. Due to health and safety reasons I couldn't use the band saw so I had to get a teacher to use it for me, I marked out the shoe winged and then told the teacher what exactly I wanted cut. I also used Hegnar saw to cut the sides of the speaker, I had used this before so knew how to use it. I've thing I did learn fro musing this was how to change the blade and how to take the blade off when cutting inside a shape. I learnt how to do this by asking the DT technician and he then showed me how to do it for future references. This was helpful to know as it would save me time instead of waiting for someone to do it for me. The pillar drill was anther main pice of machinery that's used to drill holes. This was better than using a hand drill a it as more stable and accurate. I had used this before so knew how to work it. I found myself having to use G - Clamps to hold the material to the drill bed to stop them moving and to also make it safer for me as they wouldn't spin. when using this I found the best way to get the drill bit on the correct place was to lower it and lock it in place then move the material into the correct place where I had marked it then drill through. The only problem I had with the pillar drill was trying to find the correct sized drill. It as it was always being moved and different people using it so that would waste some time. The lathe was a key tool to make my buttons. This was the most dangerous of all the tools that I used and required time and skill to use as well. I had used the lathe previously but not to do what I wanted to make. As I wasn't to sure how to use it asked what I had to do, after learning I practiced a couple if times until I was happy I could use it. I started by using a centre hole drill to drill a pilot hole into the aluminium, I then changed drill bit and drilled into a certain depth moving slowly. Working out where the correct point was I then used the cutting tool on the lathe and slowly cut across the face. This would the create a clean cut across the face of the button. I had many problems with this as I kept cutting the button off at the wrong point so was with a button with no top. I also found out that if there is to much aluminium showing and I would press the tool against it the aluminium would bend so I had to start again.
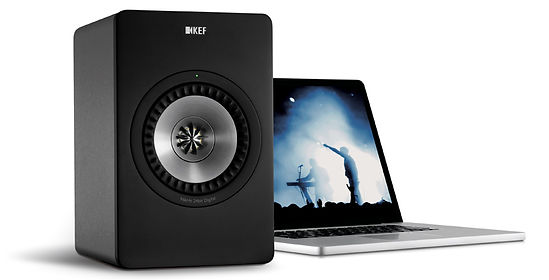